[1041]
Выделка броневых плит по способу Круппа.
В военно-технической литературе у нас почти не встречалось научных сведений об обработке брони по способу Круппа {1}. В зтом отношении можно представить вниманию читателей «Инженерного журнала» статью итальянской службы морского инженера Ugo Gregoretti {2}, переведённую на французский язык в апрельской книжке Revue de Metallurgie (Fabrication des plaques de blindage par le procédé Krupp. Тrad. de M. Stein. Rev. de Met., 1910 г., стр. 260.). Описываемый способ применяется на большом итальянском заводе Терни. По словам редакции Revue de Metallurgie, в 1904 г. французский Главный морской штаб поручил перевести предыдущие работы автора по вопросу о корабельной броне, и министр дал о них похвальный отзыв.
Здесь печатается перевод статьи, возможно близкий к французскому тексту, и в тех местах, где по мнению русского переводчика следовало дать пюяснение, сделаны соответствующие выноски, отмеченные инициалами П. С. Вставки от переводчика в тексте напечатаны курсивом. [1042] Из 37 фотографий ниже приведено только 12: такое сокращение вызвало несущественные изменения нескольких фраз и ссылок на фигуры.
Прежде чем описывать производство броневых плит по способу Круппа, мы считаем полезным дать краткий обзор выделки брони по пособу Гарвея (Harvey).
Гарвей предложил цементовать броневые плиты с наружной стороны на глубину ок. 2 см посредством углерода в твёрдом состоянии. Броневые плиты помещались парами в особые печи, между ними прокладывался слой древесно-угольного порошка или иного углеродистого вещества, затем печь разогревали и поддерживали постоянную температуру в течение от 18 до 30 дней, смотря по размерам брони.
Углерод древесно-угольного порошка проникал от поверхности плиты, с которой был в соприкосновении, на глубину 22½ см. Плиту вынимали из цементовальной печи, снова нагревали и подвергали закалке. Вследствие этой обработки, броня приобретала очень большую твёрдость на внешней поверхностиб оставаясь вязкой и тягучей в остальной своей толще.
В изломе гарвеированной стали ясно различается слой цементированный от слоя, в котором сталь осталась в мягком состоянии: зона цементации имеет блестящую кристаллическую структуру, а остальная часть излома имеет однородный вид обыкновенной мягкой стали.
Впоследствии для этой обработки применяли никелевую сталь.
Закалка всегда производится по способу английского инженера Tresider'а, состоящему в быстром охлаждении броневой плиты водяным дождём. Tresider обратил внимание на то, что при погружении раскалённого куска металла в холодную жидкость, образующийся на поверхности его обильный (теплопроводный) пар мешает соприкасаться жидкости с металлом (вследствие прилипания [1043] пузырьков пара к поверхности металла), и закалка получается не полная.
При закалке дождём пар, образующийся при соприкосновении воды с поверхностью металла, не может быть препятствием для быстрого и однообразного охлаждения плиты (так как тотчас же удаляется в атмосферу). Быстрое и однообразное охлаждение составляет необходимое условие полной закалки.
Возвратимся к процессу Гарвея. Перед закалкою броне придаётся окончательная форма на гидравлическом прессе. Так как при закалке плита неизбежно деформируется, то её снова правят на гидравлическом прессе, и эта правка тем более затруднительна, чем более форма плиты отличается от плоской. Для каждой правки нужно повторять нагрев плиты; если нагрев недостаточен, то во время выгибания плита лопается; если нагрев черезчур силён, плита отчасти теряет закалку, теряя вместе с тем свойства сопротивляться прониканию (снаряда).
Вследствие этой причины, изогнутые плиты менее сопротивляются прониканию, чем плоские или с лёгким изгибом.
Главный недостаток гарвеированных плит состоял в том, что сопротивление прониканию приобреталось только ценою большой хрупкости, которая выражалась образованием трещин при ударе снаряда, иногда повреждавших всю толщину плиты.
Плиты, приготовляемые по способу Круппа, не имеют этого недостатка, но зато проникание в них снаряда немного больше.
Сталь для броневых плит Круппа (хромо-) никелевая {3}. Для иллюстрации состава может служить следующий результат химического анализа:
Углерода . . . . . . 0,31% Кремния . . . . . . . 0,02%
[1044]
Серы . . . . . . . . 0,02% Фосфора . . . . . . . 0,016% Марганца . . . . . . 0,30% Никеля . . . . . . . 3,90% Хрома . . . . . . . . 1,78%
Эта сталь плавится в печи Мартена и отливается в чугунные изложницы в слитки, превосходящие по весу на 70% вес плиты в окончательном виде {4}.
Когда слитки охладятся до 400500°, их освобождают, поднимая изложницы передвижным краном. После этого слитки снова нагревают в печи около 12 часов до температуры 1.200° и прокатывают до толщины, немного превосходящей окончательную. Прокатка длится 4055 мин., причём температура слитка падает до 600650°C.
Полученная болванка снова вносится в печь для нагревания и, когда вся масса металла будет иметь температуру 600°, её выравнивают под прессом и затем остукивают по всей поверхности, чтобы удалить все следы шлаков и другие нечистоты.
Плиты для цементирования кладутся по две одна на другую; цементируемые поверхности расположены друг [1045] против друга и разделены стальными линейками; таким образом между плитами получается пустое пространство в несколько сантиметров высотою, ограждаемое кругом стенкою из огнеупорного кирпича. Всё это вводится в печь с подвижным подом при температуре 850900°C. В пространство между плитами впускают светильный газ в продолжение от 7 до 20 дней, смотря по размерам плиты. Светильный газ осаждает часть углерода своих углеводородов на обе плиты, и таким образом на каждой плите науглероженный слой получается глубиною около 25 мм.
В рассмотренной нами (завода Terni) плите содержание углерода в цементированной части были следующие:
От 0 до 5 мм глубины от поверхности 1,63% C. " 5 " 10 " " " " 1,20% C. " 10 " 15 " " " " 0,80% C. " 15 " 20 " " " " 0,52% C. " 20 " 25 " " " " 0,35% C.
Плита выходит из цементовальной печи при температуре 800850°C и погружается вертикально в бак с оливковым маслом: масло охлаждается циркуляцией воды, поддерживающей в нём температуру 2030°C. Эта обработка производится с целью уничтожить кристаллизацию в стали, развившуюся при продолжительном отжиге, и придать более однородное распределение углерода в плите. Плита снова затем нагревается в особой печи до температуры 660°, ниже точки превращения A1, затем погружается вертикально в бак с проточною водой, этой обработкою достигается жилковатое (fibreuse) строение в нецементованной части. (На русских броневых заводах и в Морведе был принят термин волокнистое строение или просто волокно. ava.)
Вследствие этой обработки, карбиды хрома и железа распределяются в виде мелких зёрен по всей массе стали, состоящей из раствора в железе никеля и других составляющих.
Такой структуре отвечает жилковатое сложение (texture [1046] fibreuse), дающее максимум тягучести. На образцах, вырезанных из плит, рассматриваются зёрна излома и, если нужно, повторяют закалку в масле и в воде, пока не получат искомую жилковатую структуру (тростит) {5}. [1047]
После этих двух термических обработок плита снова подводится под гидравлический пресс, чтобы придать ей желаемую форму.
Вслед затем нужно придать цементированной поверхности необходимую твёрдость, не делая, однако, всю массу хрупкою. Это достигается так называемой дифференциальною закалкой: идея её заключается в том, чтобы получить соответствующую разницу температур во всех точках толщины брони.
Для этого настилают на подвижной под печи слой сырого песка, на который накладывают плиту, подлежащую закалке, окружают её стенкой из огнеупорного кирпича, оставив открытою только цементированную поверхность. Вдвигают подвижной под внутрь печи, и когда науглероженная поверхность примет температуру от 800 до 900°C, противоположная сторона будет иметь 600650°; плиту тогда выдвигают из печи и закаливают по вышеописанному способу, то есть посредством водяного дождя, падающего на цементированную поверхность.
Таким образом получается maximum твёрдости на внешней поверхности с полной постепенностью перехода к мягкой внутренней поверхности плиты, остающейся в незакалённом состоянии. Рассматривая излом брони Круппа можно видеть весь этот переход от закалённой к незакалённой стали.
Излом плиты, подвергнутой такой обработке, cовершенно разнится от излома гарвеированной брони, в которой всегда видна линия раздела между обеими зонами стали.
Когда процесс Круппа ведут в том порядке, как только что описано, то есть с тремя последовательными термическими обработками: закалкой в масле, в воде погружением и водяным дождём, то при наблюдении [1048] излома брони заметна зона цементации на глубину от 25 до 30 мм, и уменьшающееся влияние закалки простирается на протяжении около 1/3 толщины плиты.
Английские фабриканты крупповской брони продолжают цементировать при помощи древесно-угольного порошка, как в старом способе Гарвея. Кроме того вторую закалку делают не так, как в процессе Ehrensberger'а: они доводят температуру плиты до 650° в масле и оканчивают охлаждение при помощи водяного душа. Если не производить второй тормической обработки, точно следуя способу Круппа, то, как показали опыты с пушечною стрельбой, в плитах (английского производства) обнаруживается обращение вогнутостей, отвечающих точкам удара снаряда, что указывает на недостаточное развитие волокнистости структуры в задней части плиты.
Окончтельный вид цементированной поверхности крупповской плиты довольно характерен: она шероховата и в трещинах, довольно значительных, но, впрочем, они проникают не глубже цементированного слоя и совсем не вредят защитному действию плиты: напротив того, они служат признаком хорошей цементации и большей твёрдости.
После этих различных термических обработок остаётся только выправить изгиб плить на гидравлическом прессе и затем придать размеры, указанные на чертежах. Это производится посредством строгательных и фрезерных станков, сверлильных и правильных машин и т. п.
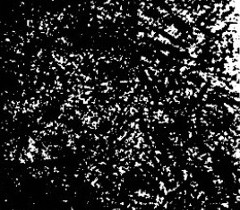
Фото 1.
Термические обработки, которым подвергают броневые плиты, могут быть легко контролируемы посредством металлографических наблюдений. Сталь в слитках имеет ясно кристаллическую структуру (как видно по фотограмме 1, увеличение 2d); сталь не обработана реактивами; на нетравлёном шлифе при небольшом увеличении можно [1049] видеть, что кристаллы расходятся лучами из нескольких точек. После полировки и протравки при увеличении в 300d видно, что эта сталь имеет зернистую перлитовую структуру, состоящую из плотно перемешанных феррита и цементита (Fe3C).
Прокатка в горячем состоянии, ведённая как мы указали, то есть законченная при температуре сравнительно низкой, уничтожает кристаллическое {6} строение стали.
При увеличении 300d после полировки и протравки видно, что структура стала более мелкозернистой, чем была раньше. Метаралы феррит и цементит более тесно перемешаны; но всё же структура состоит из зернистого перлита и феррита.
Рассмотрим теперь плиту цементированную, но ещё не закалённую; фот. 2 (увелич. 6d) снята по соседству с цементированным краем, таким образом, чтобы дать вид структуры близ этого края. В рассматриваемой плите содержание углерода варьировало от 1,63 до 0.37% на [1050] глубине в 25 мм. Последняя цифра мало разнится от содержания углерода в стальном слитке 0,31%.
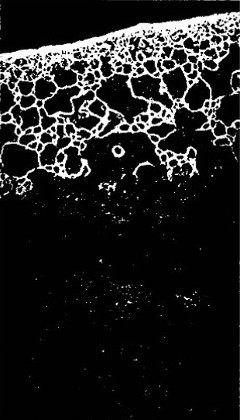
Фото 2.
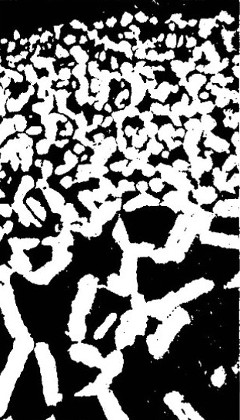
Фото 3.
Видно непосредственно, насколько изменяется структура стали вследствие цементации: образуется новая составляющая, распределённая в виде светлой сетки, которая есть ни что иное, как свободный цементит. Видно также, что эта новая составляющая более плотна к поверхности плиты, где цементация достигает maximum'а; тёмная часть, образующая как бы фон для цементита, не изменённая при цементации, состоит всегда из зернистого перлита. Эта самая область, соседняя с цементированной поверхностью, представлена на фот. 3 (увелич. 150d). Более ясно заметны сетчатые группы цементита на тёмном фоне перлита с большим преобладанием цементита.
При увеличении 150d фотография, представляющая область, расположенную на 6 мм глубины от поверхности, обнаруживает, что составляющими всегда являются цементит и перлит, но пропорция цементита сильно уменьшилась.
На 12 мм глубины фотограмма показывает, что ещё находится цементит и перлит; однако, вид микроструктуры совершенно изменился: цементит более не является в виде сетчатых образований, но просто в виде маленьких отдельных вкраплений на фоне перлитовой массы. [1051]
На 20 мм глубины (фотограмма 4, увел. 150d) содержание углирода не более 0,5%, свободный цементит совершенно исчез и уступил место перлиту {7}.
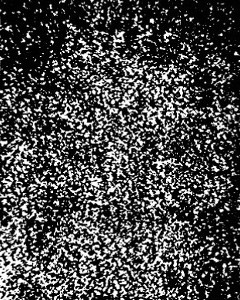
Фото 4.
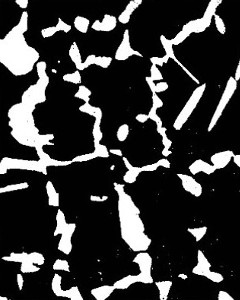
Фото 5.
На фотограмме (увел. 150d) участка, в котором содержание углерода осталось 0,31%, то есть то же, что и в слитке встречаем вместе с перлитом ферритовую сетку (белая).
Действие первой термической обработки, то есть закалки плиты в оливковом масле непосредственно после цементации, не давая ей охладиться, можно проследить на двух фотограммах, снятых в расстоянии 6 и 20 мм от поверхности цементации.
Первая из них имеет вид, подобный тому же участку до закалки (фот. 5); цементит представляет густую белую сетку, ясно выступающую [1052] на тёмном фоне; однако, если внимательно рассмотреть этот фон под микроскопом, ясно видно, что дело имеем уже с перлитом он, вследствие закалки в масле, превратился в мартенсит, представляющийся при очень большом увеличении под видом прямолинейных игольчатых волокон, располагающихся по сторонам треугольников.
Вторая фотография представляет сплошной мартенситовый фон, образованный «углеродом закала», как и на фот. 4, совсем без свободного цементита. Нецементированная часть претерпевает также значительное изменение, как можно видеть по сравнению c фотограммой, снятой до закалки. Здесь появляется новая составляющая микроструктуры: мартенсито-тростит, переходная форма между собственно мартенситом и перлитом.
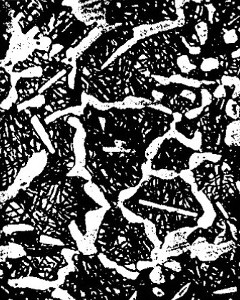
Фото 6.
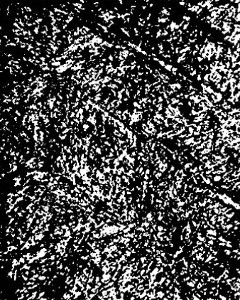
Фото 7.
Вторая термическая обработка закалка в проточной воде плиты, нагретой до температуры около 660°, вызывает новые и важные изменения в структуре. Фотограмма 6 снята на глубине 6 мм. На фот. 6 свободный цементит сохраняет тот же вид, что и до закалки, но мартенсит замещён сорбит-троститом переходная форма перлита и промежуточная между ним и цементитом. Так как тростит не совершенно исчез, можно справедливо назвать составляющую сорбо-троститом. На глубине 20 мм свободный цементит более не существует, как это было на [1053] фот. 4, виден только сорбо-тростит. На фотограмме 7, отвечающей фот. 4 заметно также большое изменение. Фон тросто-мартенситовый заменяется полностью сорбитом, происшедшим от закалки при сравнительно слабом падении температуры (фот. 7).
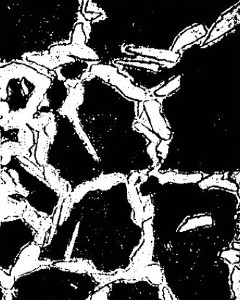
Фото 8.
Третьей и последней термической обработке, то есть при «дифференциальной закалке», отвечают важные изменения в микроструктуре.
Эти изменения становятся очевидными по фотограмме 8 при увел. 150d. Фот. 8 отвечает области, соседней с цементированной поверхностью: наблюдается ясно, что структура возвращается к той, которая была после закалки в масле. Обе составляющие цементит и мартенсит появляются снова, и фот. 8 похожа, вследствие этого, на снятую с того же участка после закалки в масле; эта закалка образовала сеть свободного цементита на фоне мартенсита с более резко выраженными углами и направлениями, указывающими на большую твёрдость.
В 20 мм расстояния от цементированной поверхности заметно также возвращение к первоначальным составляющим, то есть к мартенситу-троститу; по сравнению с соответствующей фотограммой после закалки в масле видно, насколько дифференциальная закалка придаёт большую однородность структуре из составляющих мартенсита и тростита, чем закалка в масле. [1054]
Участок, находящийся ещё в зоне закалки, но ниже зоны цементации, при рассмотрении обнаруживает сорбит с хромом или скорее с карбидом хрома в растворе. Наконец в заднем волокнистом участке плиты сорбит ещё более плотный, чем в предыдущем случае, хром также соединяется с углеродом.
По методу Бринелля были определены числа твёрдости большинства из рассмотренных под микроскопом образцов. Шарик для аппарата был взят самой твёрдой стали, 10-мм диаметра. Давление 3.000 кг.
Полученные результаты очень интересны, так как они дают очень ясное понятие о влиянии последовательных процессов и различных термических обработок на физико-механические свойства в различных стадиях фабрикации и в разных местах плиты.
Род обработки и положение образца. | Число твёрдости Бринелля. | |
---|---|---|
Отлитая болванка | 364 | первая операция. |
Прокатанная | 255 | первая операция. |
Цементованная поверхность | 362 | Цементация. |
Слой цементироованный на 12-мм глубине | 334 | |
Участок ниже зоны цементации | 282 | |
Слой, цементированный на 6 мм от поверхности, после закалки в масле | 578 | Первая термическая обработка. |
Участок на 20 мм от поверхности после закалки в масле | 555 | |
Участок за слоем цементации | 447 | |
Слой, цементированный на 6 мм от поверхности, после закалки погружением в воду | 600 | Вторая термическая обработка. |
Слой, цементированный на 20 мм от поверхности | 587 | |
Участок ниже цементированного слоя | 219 | |
Слой, цементированный на 6 мм от поверхности, после дифференциальной закалки | 611 | Окончательная обработка. |
Слой, цементированный на 20 мм от поверхности | 585 | |
Участок под цементированным слоем | 444 | |
Задний волокнистый участок после дифференциальной закалки | 285 |
Плита, к которой относится настоящее исследование, цементированая высокого качества (завода Terni), изготовленная, точно следуя способу Круппа. Для большей наглядности успеха, достигнутого в изготовлении броневых плит, помещаем следующую сравнительную таблицу (фиг. 9).
Фиг. 9.
В первом горизонтальном ряду слева направо представлены: 1 плита из однородной стали, 2 двойная стальная плита; 3 плита Гарвея; 4 плита, цементированная по способу Круппа. Предположим, что в каждую плиту ударяет снаряд 152-мм калибра со скоростью 700 м/с и, положим, что снаряд пронизывает каждую броню, доходя вершиною до задней поверхности плиты. Постепенное уменьшение толщины четырёх плит 1, 2, 3 и 4 ясно указывает на возрастающее сопротивление прониканию. [1056]
Плита однородной стали должна иметь толщину 400 мм, двойная стальная плита 320 мм, обыкновенная (не никелевая) гарвеированная 200 мм и крупповская плита только 128 мм.
Второй ряд таблицы представляют плиты крупповского типа различной толщины; толщина их соответственно равна толщине плит верхнего ряда; предположим, что в них ударяют снаряды также со скоростью 700 м/с. Сопоставление плит вертикальных рядов ясно показывает разницу в калибрах снарядов, пронизывающих плиты.
Плита № 5 Круппа толщиною 400 мм задерживает снаряд 305-мм, плита Круппа № 6 320 мм задерживает снаряд 254-мм, плита Круппа № 7 200 мм задерживает снаряд 200-мм. [1057]
Также интересно рассмотреть опыты орудийной стрельбы по броне.
Первый элемент, который необходимо принять во внимание при опытах стрельбы, это скорость снаряда при ударе; дистанция орудия до плиты безразлична, достаточно сообразовать величину заряда на данную дистанцию.
Скорость снаряда при ударе можно вычислить (даже установить опытным путём) с большой точностью для каждого типа пушек и каждого веса заряда и проверять во время стрельбы имеющимися для этой цели инструментами. Эта скорость определяется по таблицам стрельбы, чувствительно схожим во флотах всего света. Единственная разница в этих формулах это в численном коэффициенте, и тем опыт строже, чем коэффициент выше. Можно делать действительное сравнение между двумя плитами, только увеличивая постепенно скорость удара, пока снаряд не будет пронизывать плиту; только в этом случае можно признать лучшею из двух ту плиту, которая потребует большой скорости удара; и разность между обеими скоростями образует единственную возможную меру для оценки способности защищать у обеих испытываемых плит.
Также необходимо принять в расчёт тип и качество снаряда: все современные снаряды одной формы цилиндрическое тело с оживальной головой, с очень острым концом. Внутри снаряда имеется камера, содержащая сильно взрывчатый заряд; при равенстве наружных размеров, чем камера больше, тем стенки снаряда тоньше.
Снаряды для пробивного действия можно подразделить на две категории: фугасные и бризантные. У обоих внешняя форма почти одинакова, но у фугасного снаряда зарядная камера значительно меньше, чем у бризантного (фиг. 10). (Тут, видимо, в силу двойного перевода с итальянского на французский, а затем с французского на русский произошла подмена терминов, и речь, естественно, должна идти о бронебойном снаряде, более прочном, с более толстыми стенками и меньшим содержанием взрывчатого вещества, и фугасном снаряде, вмещающем больше взрывчатки, но в силу этого имеющим гораздо меньшее бронебойное действие. На фиг. 10 слева разрез фугасного снаряда, справа бронебойного. Качество картинок, увы, пока такое, как есть. ava.)
Фиг. 10.
Легко понять, что толщина стен имеет большое влияние на пробивную способность снаряда.
Как пример, мы упомянем о следующем факте: недавно у нас в руках была фотография изогнутой плиты, испытанной на одном из иностранных полигонов. [1058] Испытательная комиссия признала опыты очень удовлетворительными, и фабрикант не преминул прибегнуть к широкому распространению этих фотографий в качестве рекламы. Против плиты было выпущено 3 снаряда с ударной скоростью, значительно превосходящею получаемую при опытах в итальянском флоте в Мужиано. Все три снаряда разбились о плиту, не причинив ей никакого вреда. Результаты казались действительно необычайными, но когда мы узнали веса выпущенных снарядов, то заметили, что они значительно ниже обыкновенно употребляемых снарядов.
Сравнительно простой подсчёт позволил нам вывести из разницы между весами, что в употреблённых снарядах стенки были приблизительно на 1/3 тоньше, нежели [1059] у наших снарядов. Полученные результаты произошли оттого, что выпустили против плиты снаряды с тонкими стенками, для которых увеличение скорости ещё больше благоприятствует броне, способствуя разбиванию снаряда при ударе о плиту.
Это рассмотрение позволяет нам привлечь внимание на затруднительность вывода заключений по опытам стрельбы для испытания броневых плит на иностранных полигонах.
Обратимся наконец к качеству снарядов. В этом отношении флоты разных стран в течение последних лет сделали быстрые успехи: наконечник из мягкой стали на голову снаряда увеличил на 20% cпособность проникания снаряда при равенстве прочих условий, кроме того качество металла снарядов значительно улучшилось.
При испытании стрельбою плиты укрепляются к щиту в существенной части, состоящему из подушки, образованной толстыми дубовыми досками, опирающимися на металлическую арматуру. В Италии толщина дубовых досок 15 см, в Германии и Аyглии в общем 60 см и часто даже 1 м.
Такая большая толщина щита очевидно ставит плиту в лучшие условия, так как вся система более упруга и живая сила удара поглощается большею массой, принося меньше вреда броне. Испытание плит в итальянском флоте производится тремя выстрелами со скоростью, указанною в контракте, и ни один снаряд не должен пробить щит.
Во Франции один снаряд выпускается с максимальной скоростью, два другие с меньшею.
В гарвеированных плитах допускают трещины, так как они неизбежны по самому способу фабрикации. Как на пример, мы укажем на гарвеированную плиту 20-см толщины, испытанную стрельбою трёх снарядов калибром 203 мм с толстыми стенками высокого качества и вонзившимися со скоростью 560 м/с.
Фото 11.
По условию в контракте снаряд не должен был [1060] пробивать плиты и ни один осколок плиты не должен вываливаться на землю.
При первом выстреле образовались три трещины, расходящиеся от точки удара. При втором выстреле первоначальные трещины увеличились и появились три новых; при третьем выстреле шесть существовавших трещин расширились и появились ещё четыре новые (ф. 11). Однако, ни один снаряд не прошёл сквозь плиту и ни один кусок её не вывалился из щита. Плита принята, она удовлетворила в действительности всему, на что можно надеяться при плите из никелевой гарвеированной стали. Напротив, плита, цементированная по способу Круппа, той же толщины, испытанная в тех же условиях, задержала три выпущенных против неё снаряда, не обнаружив ни малейшей трещины (ф. 12).
Фото 12.
Можно сказать, что защита, даваемая обеими бронями, чувствительно одинакова, однако крупповская плита остаётся [1061] после стрельбы в лучших условиях, чем гарвеированная. Для опытов с плитами на всех полигонах Европы берутся снаряды без наконечников, только в Америке в некоторых случаях испытывают броневые плиты снарядами с наконечниками, переводя в этом случае значение ударной скорости. В таких условиях американские опыты вообще более благоприятны, чем европейские, так как снаряды с наконечниками реже причиняют трещины, даже при хрупких плитах.
П. Сахаров.
Техническая лаборатория
Н. И. А.
15 Мая 1910 года.